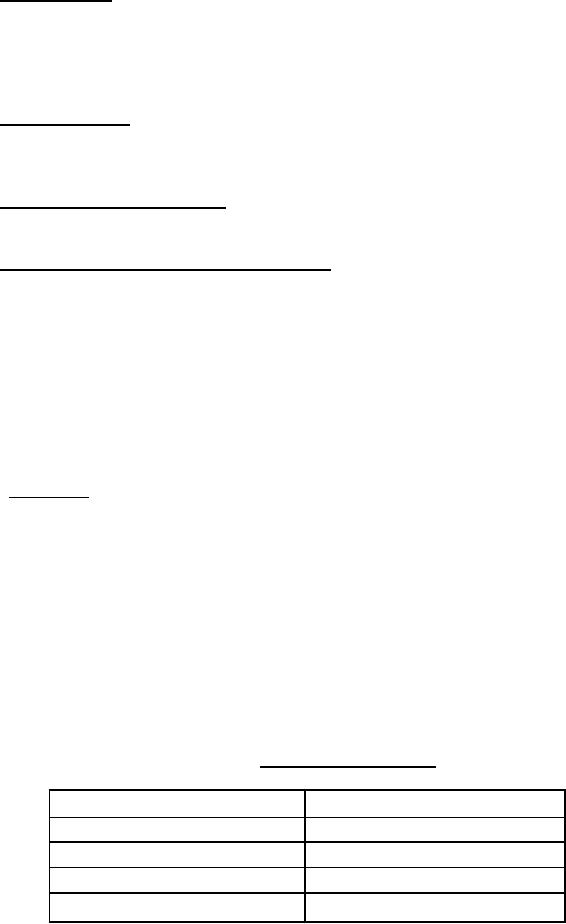
MIL-PRF-27720G
3.6.6 Vapor vent line. The vapor vent line shall permit the tank assembly to cool down within
15 minutes and allow filling flow rates up to and including 50 gpm without the inner shell vapor
pressure exceeding 15 psig, when the tank assembly is subjected to the conditions and tests
specified (see 4.5.11.3). The vent line shall allow venting of liquid when the inner shell is being
filled and the tank contains between 400 and 410 gallons of liquid.
3.6.7 Vacuum retention. The tank assembly, after evacuation of the annular space, shall not
show any increase in absolute pressure attributable to leakage or outgassing within 7 days (168
hours) when subjected to the tests specified (see 4.5.7.1).
3.6.8 Dissimilar metal vacuum joints. Any dissimilar metal vacuum joints used in the tank shall
withstand thermal shocks, and axial and lateral vibration as specified (see 4.5.16.1.1).
3.6.9 Shutoff and control valve cycling and leakage. The valves shall withstand a closing torque
of at least 300 in.-lb per inch of nominal size, with the valve bodies at either ambient temperature
or the atmospheric pressure boiling temperature of liquid oxygen or nitrogen. When
subsequently closed with a torque of 60 ± 5 in.-lb per inch of nominal size and a pressure of 50
psig applied to the inlet, the valves shall not leak more than 2 cubic inches of free air, oxygen, or
nitrogen gas per hour per inch of nominal size. The valves shall be capable of not less than 2000
cycles of operation when subjected to a differential pressure of 50 psig while closed, including at
least 1,000 cycles at ambient temperature and 1,000 cycles with the valve body at the
atmospheric pressure boiling temperature of liquid oxygen or nitrogen for Type I or Type II tank
valves, respectively (see 4.5.13).
3.6.10 Line filters. The liquid fill line and the liquid servicing line shall each have a filter for
the filtering of all liquid flowing into and out of the inner shell. Filters shall be of the in-line
configuration conforming to USAF 68B39474. Each filter shall be installed such that it is
readily accessible for inspection, cleaning, or removal. Sintered or powdered material shall not
be used unless provisions are made to prevent media migration. The proper direction of flow
shall be plainly marked on each side of the filter. The filters shall be a non-bypass type and shall
withstand a pressure drop of 50 psi across their elements. Each filter shall remove 98% by
weight of all particles whose smallest dimension is 10 microns or greater (10-micron nominal
rating). The filter shall further remove all particles whose smallest dimension is 40 microns or
greater (40-micron absolute rating). In addition, the filter shall be capable of a liquid oxygen
flow rate of 50-gpm at a maximum pressure drop of 3 psig, having previously ingested a
minimum of 5 grams of particles of the sizes shown in table II (see 4.5.12.1, 4.5.12.2, 4.5.12.3).
TABLE II. Particle size distribution.
Size of Particle (microns)
Percentage by weight (± 3%)
10 to 20
36
20 to 40
24
40 to 60
16
Over 60
24
13
For Parts Inquires call Parts Hangar, Inc (727) 493-0744
© Copyright 2015 Integrated Publishing, Inc.
A Service Disabled Veteran Owned Small Business